Industrial bakeries
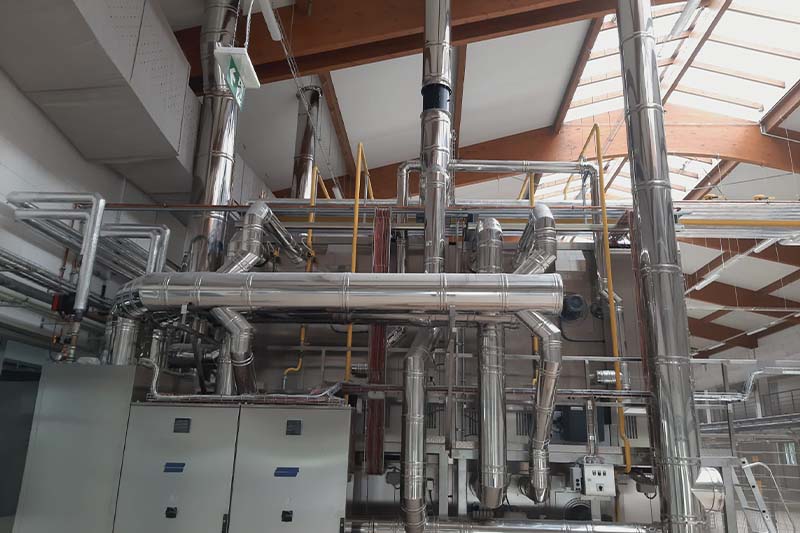
In the field of industrial bakeries, no project is the same as another. Therefore, detailed, professionally competent advice on bakery projects and consideration of various customer requirements during the planning phase are essential to achieve the right exhaust concept and the best possible solution.
Exhaust systems for ovens in industrial bakeries must meet special requirements, as each oven typically has four pipe connections: a flue gas pipe, a steam pipe, a fresh air pipe for the oil/gas burner, and an exhaust pipe for the hot air that can escape when the oven door is opened.
The hot exhaust gases from the various burners, as well as the steam (moist air from the oven), are usually directed via a flue gas or steam collection channel to a heat recovery system in the form of a cascade system.
Since steam contains a high percentage of moisture due to the baking process, the tightness of the pipe system is particularly important in this case. The Jeremias element systems ensure this with a plug connection featuring an internal special seal and an external clamping band.
To minimize heat loss on the way to the heat exchanger, an insulated, double-walled stainless steel chimney is typically used for the flue gas pipe.
While this exhaust system is primarily used in the main chimney, it is recommended to use a pressure-tight, single-walled system for the fresh air and exhaust ducts.
Jeremias offers flexible solutions for various requirements and planning designs. With the largest product range on the market, Jeremias exhaust systems are compatible with all flow-through ovens, deck ovens, and more available on the market. Our competent technical consultants have years of experience in the bakery sector and have successfully implemented many large and challenging projects.